Lagging plays a crucial role in protecting the pulley on your belt conveyor system, increasing belt friction and reducing abrasive wear as well as material build-up. It is the layer of material bonded to the shell of a conveyor pulley, typically covered in some form of rubber, ceramic, polyurethane, or other materials. The material chosen is highly dependent on your specific application, as explained in our blog on how to choose lagging for your operation.
And with polyurethane lagging growing rapidly in popularity, we decided to take a deep dive into the pros and cons of polyurethane lagging versus full ceramic lagging. Keep reading as we weigh up the facts.
The Pros and Cons of Polyurethane Lagging on Your Conveyor
Also known as plastic lagging, polyurethane has been gaining popularity in non-drive pulley applications where there are concerns about carryback buildup between the belt and lagging. It can be applied as a sheet or strip, either bonded with rubber-backed polyurethane or cast directly on the pulley shell. Compared to rubber lagging, it has a three to five times longer service life and provides higher abrasion resistance. The low coefficient of friction makes polyurethane lagging kind to the belt bottom cover, making it the ideal solution for belts with premature wear. Polyurethane lagging also poses very little risk of damage to the belt cover. It is commonly used on bend pulleys where there is slippage between the belt and lagging surface.
However, cast polyurethane lagging is very expensive to apply and extremely difficult to repair, it is generally only used when rubber or ceramic lagging has proved less serviceable. Furthermore, polyurethane lagging lasts a maximum of five years before the pulley needs to be refurbished. As mentioned, this is a very costly and labor-intensive procedure, hence polyurethane is recommended to be used only for bend pulleys and non-drive pulleys on turnover conveyors.
The Pros and Cons of Ceramic Lagging on Your Conveyor
Ceramic lagging is popular in applications where belt slip or high wear are a concern as it is more durable than rubber. The most common types of ceramic lagging utilize either smooth or dimpled ceramic tiles, both offering a significant increase in friction, grip, and tracking of the belt.
Ceramic lagging has four main advantages over other types of lagging:
1) The ceramic tiles are extremely resistant to abrasion so it can handle harsher materials and the dimples can significantly improve traction for drive pulleys.
2) The amount of coverage of ceramic on the surface of the lagging can be customized to your application and requirements, with options to feature 13%, 39%, and 80% ceramic coverage.
3) Ceramic lagging has a greater service life, which reduces lagging wear significantly.
4) Smooth ceramic lagging is the optimal choice for non-drive head pulleys; it has a flat, even surface for the belt and belt cleaners to run efficiently.
There aren’t many negatives to consider when installing ceramic lagging, but it is best to get expert help when choosing the right type of lagging for your belt conveyor system. For example, depending on the conveyor design when choosing dimpled ceramic lagging, belt clawing or bottom-cover damage can be displayed if there is belt slippage present, as the dimples can claw the backside of the belt. So, it makes sense to talk to a trusted expert when deciding what lagging is best for your system.
So, which belt conveyor lagging is best?
Polyurethane and smooth ceramic lagging are both acceptable choices when deciding which lagging is best for your non-drive head pulley. However, if you want to make a cost-effective decision that will boost your productivity in the long term, full ceramic is the optimal choice.
In most applications, polyurethane lagging has a maximum life span of five years, while smooth ceramic lagging in the same application has been proven to last at least 20 years. Not only is the initial product and installation cost much cheaper; you’re also saving yourself the cost of replacing the lagging at least three to four times over the service life of the pulley.
In May 2001, Flexco installed full ceramic Flex-Lag® Pulley Lagging in iron ore as part of the site spec. Today, 20 years later it is still in perfect condition as seen in the image below. Read the full case study here.
Get an expert to assess your lagging
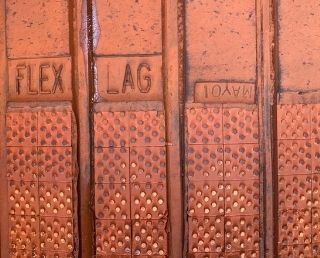 |
Full Ceramic Flex-Lag® installed in May 2001 |
Despite popularity and price, choosing a type of pulley lagging must come down to your specific application: including conveyor design, product abrasion, pulley type, and belt speed. It is vital to your operation to have an expert determine these factors and weigh up which material is most suitable for your conveyor pulley.
At Flexco, we truly believe in finding the best solutions and technology for your specific application and operating conditions. Sign up for a free assessment and a local representative will come out to your operation and help you choose the right lagging solutions for your belt conveyor system.
Authored by: Phil Dreghorn, Regional Manager
Dreghorn joined Flexco in 2003 as Queensland’s Sales Manager. Prior to Flexco, Dreghorn held various roles in the belt conveyor system industry involving conveyor maintenance and belt splicing and has a special interest in lagging products. Dreghorn holds qualifications as a boilermaker and belt splicer and completed training as a Work Health and Safety Officer.