With the pandemic came a boom in e-commerce. In such a changing and progressive world, events like the pandemic have created extreme exponential growth in not only the parcel handling industry but distribution and fulfillment centers where thousands of items are individually sorted and distributed to customers. According to Tech Crunch, citing data from IBM’s U.S. Retail Index, the pandemic accelerated the shift to e-commerce by 5 years. It helped drive e-commerce sales for Walmart by 97 percent, and Target set a sales record as its same-day fulfillment services grew 273% in the 2nd quarter of 2020.
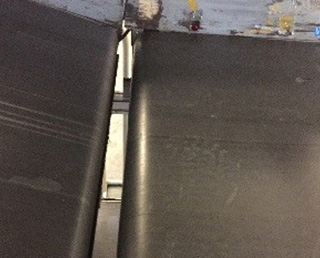 |
An unguarded belt conveyor transfer can lead to product loss. |
However, with rampant and growing success, come challenges as well. The need to be competitively productive is at an all-time high, with every minute of lost productivity costing major players in the industry hundreds of thousands of dollars. The question is, “How can you solve your pain points in a quick and effective manner?”
One of the biggest challenges these industries face is how to maintain a conveyor belt that runs smoothly and without interruption. Conveyor transfer gaps are areas contributing to one of the biggest causes of conveyor downtime in the parcel and logistics industries. The gaps can lead to Foreign Object Debris (FOD) and small packages being caught in the opening, which leads to conveyed product damage or product loss. This can be especially problematic when working with ever-tightening windows of time provided to get orders out to customers, sometimes delivering that same day.
Why homemade solutions for belt transfers aren’t always effective
The solutions available to the above-mentioned issues have been limited, with maintenance personnel often having to resort to homemade devices made from ultra-high molecular weight (UHMW) plastic. However, there are serious implications involved with this practice.
The first and most prevalent issue with the homemade UHMW solution is that it is common to see gaps of 6mm or more between the belt and UHMW plates. Installers are taught to do this because of the unforgiving nature of the solid UHMW plate, which is generally mounted to a stiff piece of angle iron. The required added gap allows foreign object debris (FOD) to make its way into the space between the UHMW plate and the conveyor belt surface, causing progressive damage to the belt, conveyor components, and even the conveyed package.
When this happens, there could be significant damage to the belt, or to conveyor system components. The damage can require hours, if not days, of downtime to make the necessary repairs. On top of this, the single UHMW plate can warp over time, creating a wavy plate with even larger gaps, opening up the opportunity for FOD and/or small packages and polybags to become trapped, further adding to the issues caused by this old technology.
The second issue is the cost and time associated with traditional UHMW transfer plates. Most of these plates, while relatively cheap to produce, have a life expectancy of only six months. Due to their short life span, time and resources must be allocated to replace the plates regularly. The installation process can be a timely and tricky procedure. As installation of the UHMW plates is often complex, requiring artisan-like custom fitment, it is not uncommon for the plates to be installed incorrectly, meaning additional hours of maintenance work in the future.
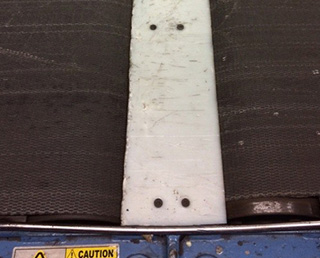 |
A homemade transfer plate sits on the belt. |
A third, and very important, issue is safety. While traditional UHMW transfer plates generally cover the gap between two conveyors, they are not effective at reducing nip hazards or pinch points in the transfer area. As noted earlier, the solid UHMW style of transfer plates are installed with clearances between the belt and the plate that sometimes exceed recommended OSHA guidelines, making them a serious safety hazard for employees working near the conveyor transition area.
Homemade/OEM-installed UHMW plates are an inefficient solution resulting in unscheduled downtime, lost productivity, potential harm to your belt, and reduced safety for your workforce.
An Engineered Solution to Transfer Point Product Loss
What can I use instead of homemade UHMW plates? The answer is easier that you may think thanks to newer, engineered solutions that provide longer wear life, meaning less maintenance and downtime. Looking for even less of a maintenance headache? An engineered solution with segmented plates is an attractive choice. In a scenario where a piece of FOD is caught in the transfer, a segment can dislodge, leaving the rest of the plat intact to do its job. Even better … replacement segments are easy to install, which means your downtime can turn from hours to seconds. Engineered solutions also come in a range of sizes, meaning the perfect solution for your site is easy to select and incorporate into your belt conveyor system.
A Flexco Solution - Segmented Transfer Plates
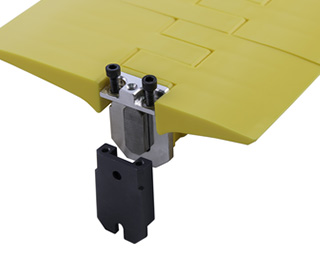 |
Flexco Segmented Transfer Plate |
In such a rapidly changing industry with an increasing demand for efficiency and volume, it may seem daunting when issues like conveyed package or product loss are encountered on your belt conveyor system. Luckily there is light at the end of the tunnel.
Recently a parcel handling facility discovered that a number of packages, including a vehicle tire that had fallen through the transfer point, created a significant safety risk as well as a loss of productivity. In this case, our product experts at Flexco were able create a fully-custom solution using two separate sets of transfer plate bars. Thanks to the installed Segmented Transfer Plate, a functioning transfer between the drawbridge and stationary conveyor, with a paper-thin gap between the belt and new transfer plates, was attained. As an added bonus, the plates are yellow, a huge benefit seen by the maintenance managers when it comes to safer operation. While the plates now stops packages and other items from dropping into the gap, they also reduces the risk of operators being injured at the transfer point by the moving conveyor belt. To read more about this success, click here.
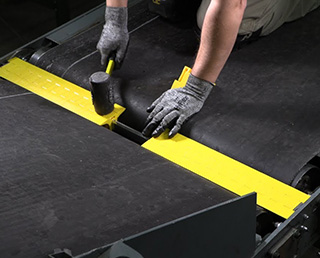 |
A Flexco Segmented Transfer Plate is quickly and easily installed on a belt conveyor system. |
The use of innovative technology like Flexco Segmented Transfer Plates can create a complete solution for product loss and increased operator safety at the transfer point. With this solution, each plastic segment is positioned directly on the belt, which prevents product ingestion and reduces nip points and pinch hazards. When installed properly, the light seal against the belt prevents FOD from becoming lodged between the belt and the plate. In the rare event FOD does get in between the segment and the belt, the segment will lift, allowing smaller FOD to fall through or eject under more extreme circumstances. The plate can then be repaired in seconds by simply snapping a new segment in place, resulting in no damage to the belt, conveyor structure, or packages, while significantly reducing conveyor downtime.
Flexco Segmented Transfer Plates Increase Productivity Belt Conveyors
If you're ready to implement Flexco Segmented Transfer Plates and get rid of all the headaches caused at your transfer points, request an assessment to get in touch with one of our experts. We’ll come to your facility and take a look at your transfers to determine the best path to increased output and maximum productivity.
Stewart has been with Flexco for 30 years, working in various roles from customer service, to manufacturing, to training and new product development. As Industry Manager, Stewart thoroughly researches target industries, creating programs to support each industry and identifying customer issues, as well as potential product solutions. Stewart currently leads the development of the Parcel Handling Industry Program and is responsible for ensuring that Flexco is positioned to serve the needs of our global customers. Stewart earned a bachelor’s degree in Marketing with a B2B specialty from Davenport University.