According to the National Institute for Occupational Safety and Health (NIOSH), mining represents the industry sector with the highest fatal injury rate, more than five times than the national average?
NIOSH found 26 occupational fatalities and 4,517 non-fatal lost time injuries were reported in 2015 to the Mine Safety and Health Administration. Sprains and strains topped the list of the 44.4% of non-fatal injuries reported, with the back being the most frequently reported body part resulting in 50,320 days lost from work. The consequences of burnout due to these stressors are potentially problematic for both the individual and the organization. Burnout can result in work of less quality, job turnover, absenteeism, and low morale.
Why are we sharing this info with you? We want you to better understand the importance of limiting every opportunity that could put your worker’s safety at risk, and severely affect your productivity. While you can’t control all the variables that come with working in tough conditions – inclement weather, abrasive materials, etc. – you can control how you prepare for safe belt repairs.
Ultimately, safe conveyor belt maintenance starts with choosing the right tools – that have been engineered with safety as a top priority. So, here are the top three tools that will make your belt repair process easier, faster, and safer.
Tool 1: Conveyor Belt Lifters
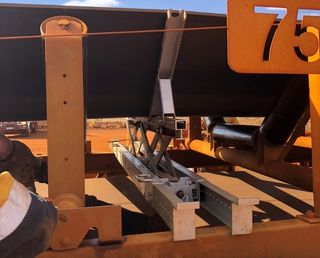 |
The Flex-Lifter™ Belt Lifter holding a conveyor belt. |
Lifting a tensioned conveyor belt out of the way to do maintenance work is a difficult job. It can be both time-consuming and dangerous for operators. When lifting a conveyor belt without a safe support tool, there is a high risk of injuries because improper tools can fail, you’re working with suspended loads, and workers can become fatigued from manual handling.
The Flex-Lifter™ Belt Lifter puts an end to pry bars and manual lifting. It is designed to support and lift conveyor belts up to 96” wide and has a safe lift rating of 6000 lbs. The versatile tool has adjustable wings that make it easy to lift troughed or flat topside belts. It truly makes a difficult and hazardous job easier and safer – check it out for yourself in this video of the belt lifter in operation.
Tool 2: Engineered Belt Clamps
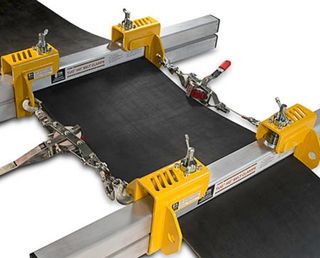 |
TUG™ HD® Belt Clamps complete set up. |
In addition to locking and tagging out your belt conveyor system and wearing proper PPE, clamping your belt properly is one of the most important steps you can take to avoid a catastrophic event. It doesn’t matter if you are a half mile off the ground, or a half mile underground, clamping is one of the most important safety precautions you can take during a repair.
Keep in mind that serious injuries are possible when clamping is done without using the proper tools and products – which has been explained in our blog homemade VS engineered belt clamps. TUG™ HD® Belt Clamps are designed to secure the belt by clamping over it for greater strength in higher-load applications rated from 6- to 8-tonnes, making them ideal for mining applications. They are third-party tested, and the safety factors of clamp ratings meet or exceed industry standards. It’s time to say goodbye to homemade devices like c-clamps, lumber, and chains.
Solution 3: Electric Belt Cutters
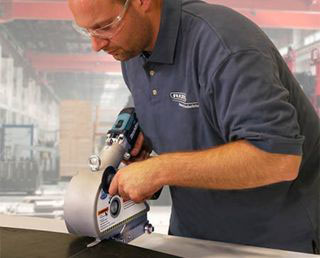 |
Cordless Belt Cutter. |
Utility knives simply can’t provide the same level of safety, speed, and accuracy when cutting belts. Power assisted belt cutters minimize the danger of accidental injury during the belt cutting process and provide a smooth, accurate cut. For example, a safety-conscious power plant replaced their utility knives with a cordless belt cutter that reduced their average finger splice time to only 20-25 minutes and required only one worker to complete the job.
Available in both corded and cordless versions, Flexco Electric Belt Cutters quickly and easily cut all types of belting from the softest of natural rubbers to the hardest constructed solid woven PVC and fabric plied belts. The tool cuts up to 2” on rubber belts and up to a maximum 360 P.I.W. on PVC belts. Operators are protected by a spring-loaded blade guard and can feed the cutter into the belt with minimal effort because of the sealed ball bearings.
TIP: Always square your belt
Effective belt repairs start with straight, square cuts. Squaring your belt ends is a job that requires only a few minutes of your time and offers real paybacks in extending your belt splice life. Here is a step-by-step guide on how you can properly square your belt before cutting.
Train your team
Even well-designed and well-built maintenance tools can malfunction or become hazardous in the hands of an inexperienced or untrained user. Operators must be thoroughly trained before operating conveyor belt lifters, belt clamps and electric belt cutters. Flexco offers free conveyor belt repair training that includes preparing belts for safe repair. Book a free demonstration here to ensure you provide maximum safety for all operating personnel, and to get a maximum benefit from your equipment.
Authored by: Ellaina Mackay, Flexco Australia Product Manager
Mackay joined Flexco in 2018 as the Marketing Communications Coordinator. Over her years working at Flexco she has proven her expertise and knowledge across the mining and metals industry, leading into her new role as the National Product Manager in 2021. She now manages the overall product strategy for Flexco Australia.